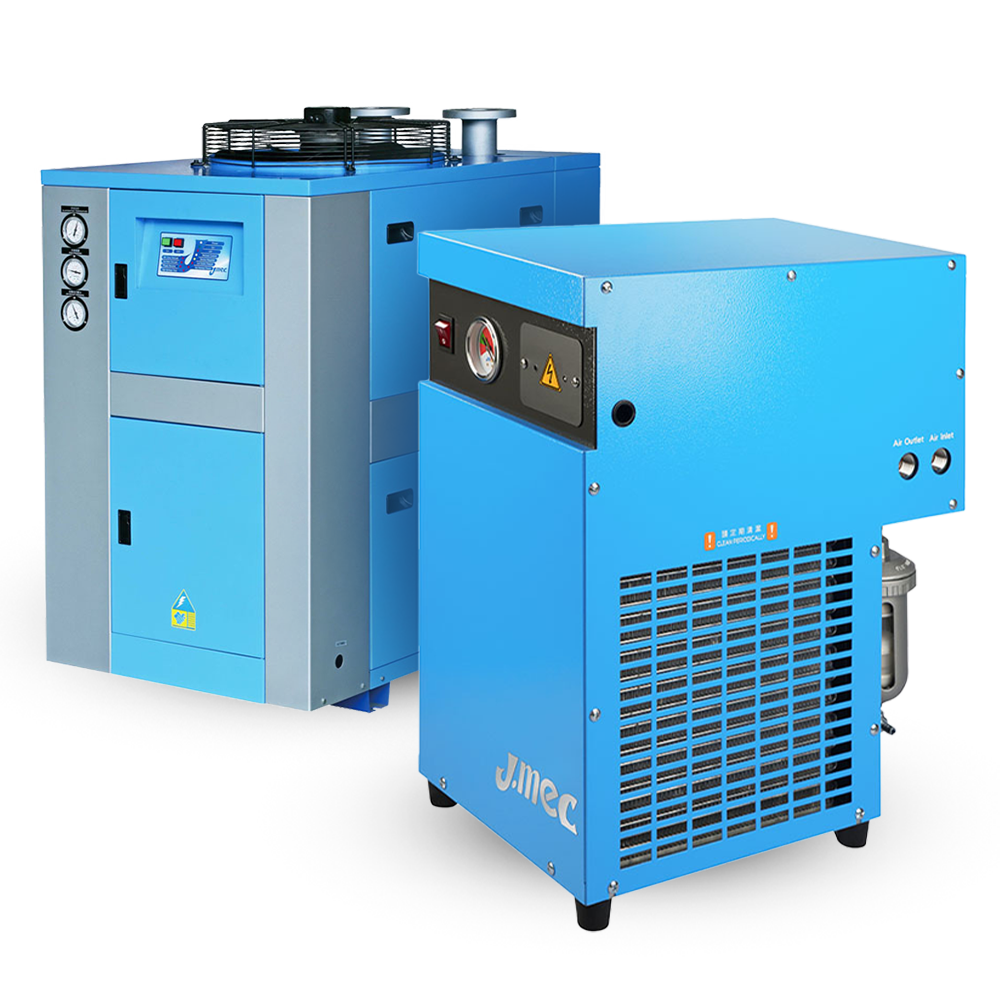
Compressed air dryers and treatment systems to protect pneumatic equipment
Untreated compressed air contains water, dirt, oil and other waste particles which will mix together to form unwanted abrasive slurry, this abrasive slurry, generally acidic in nature, will cause wear in pneumatic machinery, valves, orifice etc. causing frequent high maintenance breakdowns and costly air leaks. A typical compressed system wastes approximately 35% air due to “leakages” which are mainly caused due to corrosion.
All ferrous metals need two components to cause corrosion; moisture and oxygen. Untreated compressed air contains both. This corrosion attacks piping, joining elements and also the equipment where compressed air is being used. The end result is leakages and malfunctioning of expensive equipment. Rusting commences on ferrous metals when the relative humidity (RH) of air exceeds approximate 30%. However, at this point oxidation is slight and “serious” corrosion starts when RH exceeds 60%. It therefore seems very logical to keep RH value in the air at or below 60%.
It is thus very essential to install a suitable Air Purification System to meet individual needs.
Advance Cooling Systems Pvt. Ltd. has teamed up with the experts in this field, M/S Jia Meng of Taiwan (with heavy presence all over the world} to give you a Complete Air Purification System (CAPS}.
Salient Features & General Characteristics:
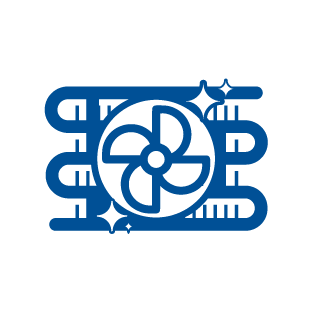
A completely automatic self contained Logic controller with standard wiring requiring “no adjustments”.
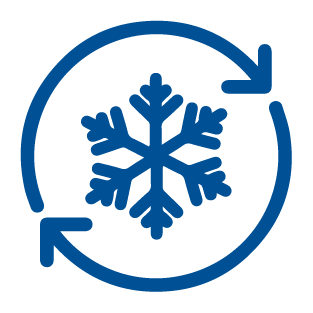
A”pre-cooler” with excellent air distribution and very low pressure drop, built in the refrigeration condenser coil, with thermal isolation, to cool the incoming compressed air
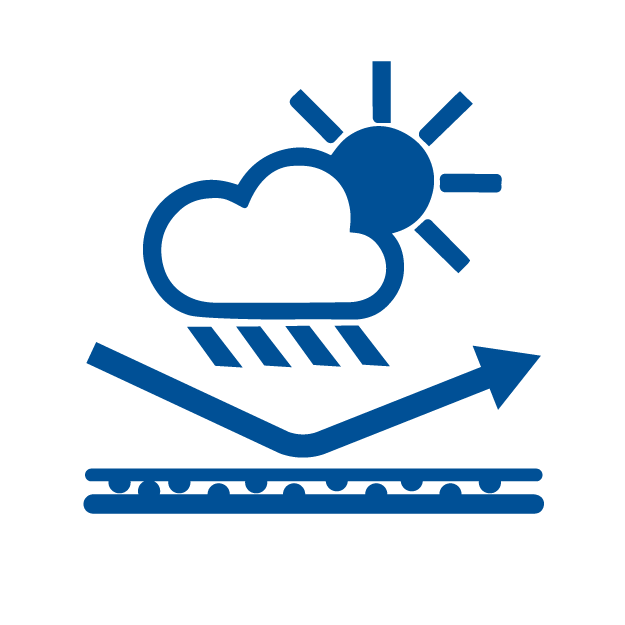
A compact Stainless steel (rust free) high pressure vessel. Two-in-one design containing Air-to-Air heat exchanger and a high efficiency evaporator.
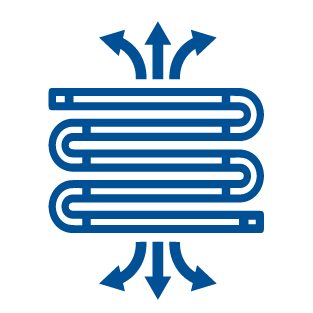
Bronze tube air-to-air heat exchanger with reverse channel for efficient cooling, increased outlet air temperature, and reduced energy use.
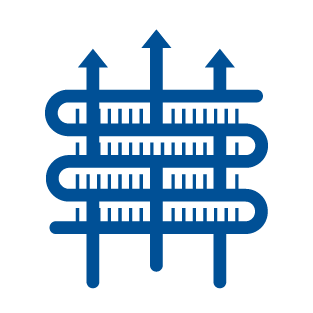
Evaporator made out of wave type aluminium fins with diversion plates to increase the contact surface of air and refrigerant so as to give optimum cooling efficiency.
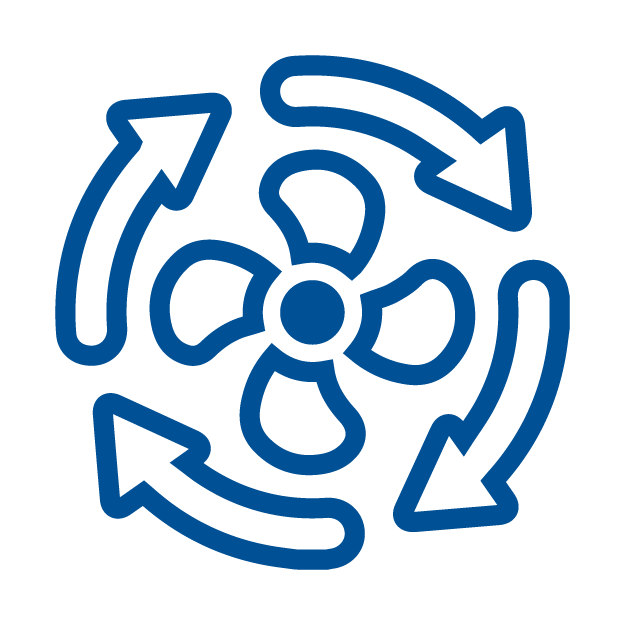
A very large intake condenser with “blow-up” design for better heat rejection and good ventilation.
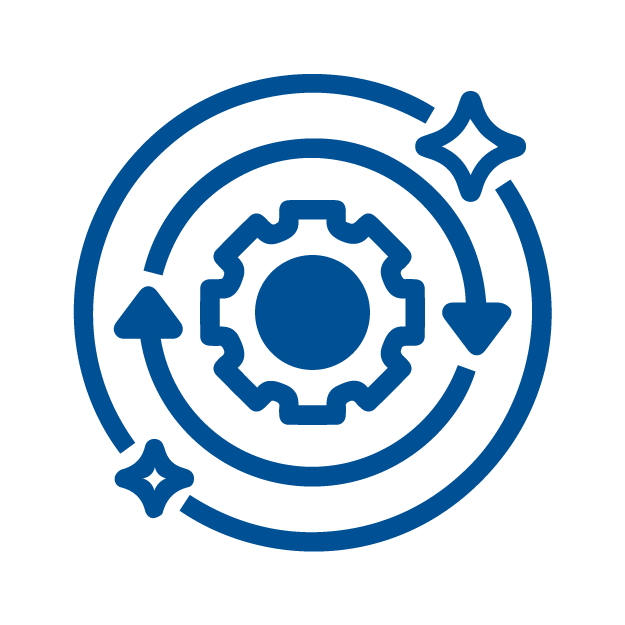
A “motor-driven” (no more burnt solenoid coils) timer controller electronic drainage with anti-blockage large ball valve.


Technical specifications
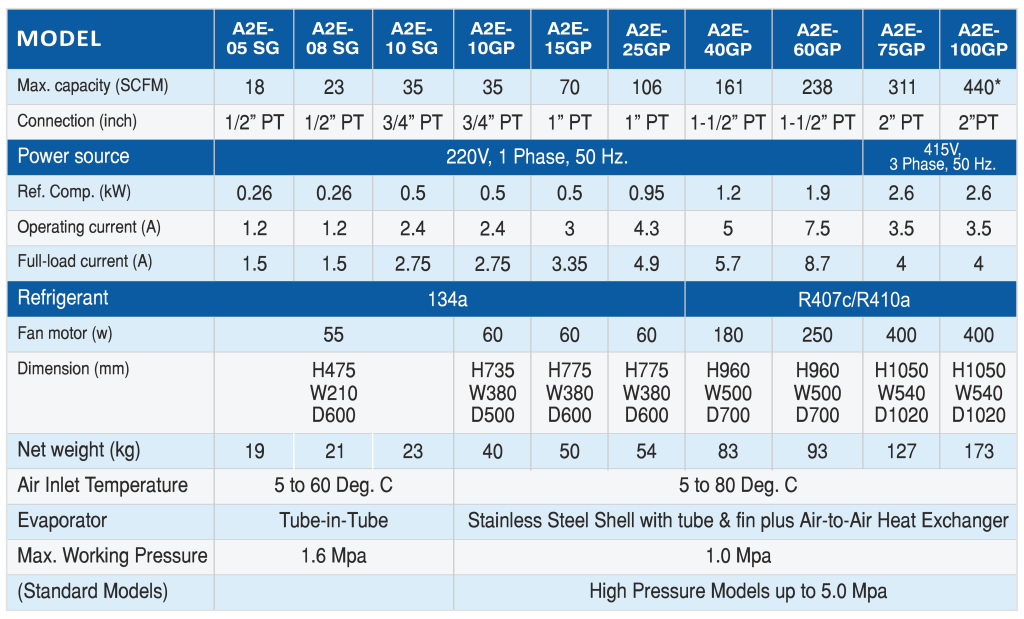
Get In Touch
Interested in our product?
Answer a few short questions and we’ll get in touch with you!